Leadership
Ranco Fertiservice continues its daily operations under the leadership of President/COO, Nate Wittmaack, and CEO/CFO, Jeff Christians. Their guidance assures that everyone at Ranco consistently maintains the same goals and mission for our customers. As an employee-owned company, much of their time is devoted to helping each employee focus on customer satisfaction and work towards ‘perfection of the process’. Nate and Jeff also get involved with the daily operations and often work directly with our customers.
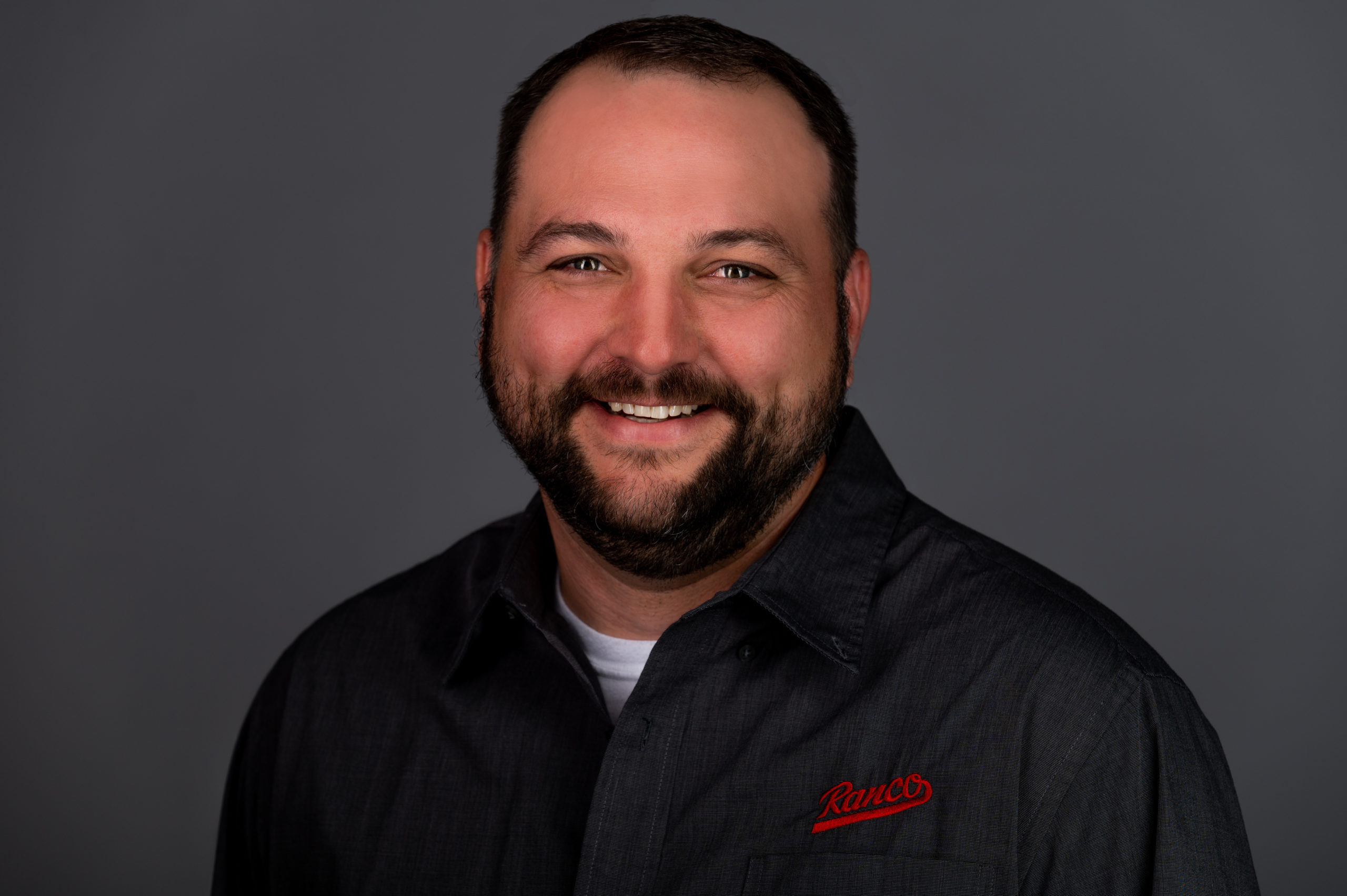
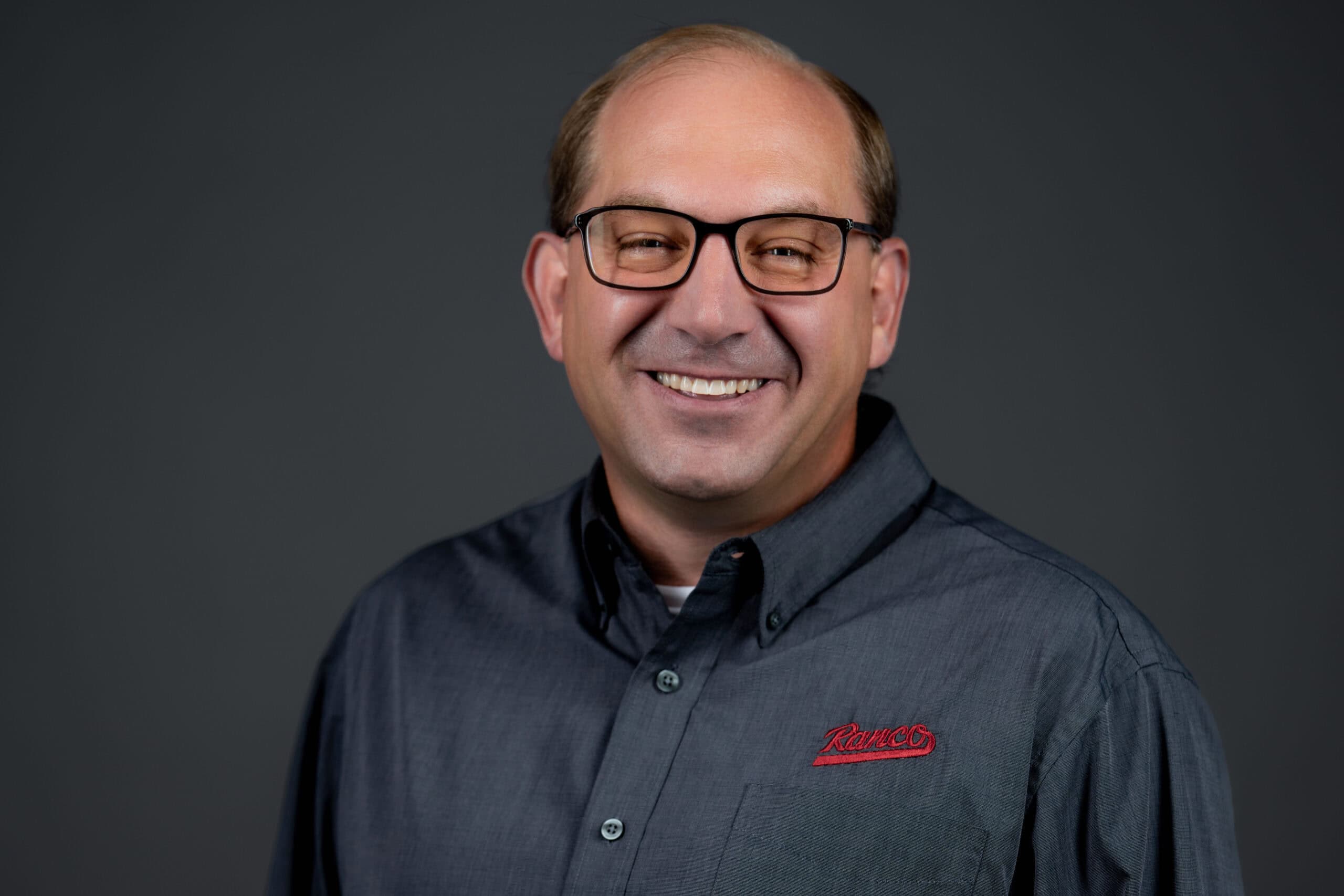
Office
Administrative Staff, Project Managers/Sales, Drafting and Engineers are all housed under the same roof. Being together in an open environment makes project coordination much easier and more efficient. The daily communication amongst the Ranco team is always continuous and fluid. From the production staff, road crew and parts department, to the engineers and sales group, open discussion is always encouraged.
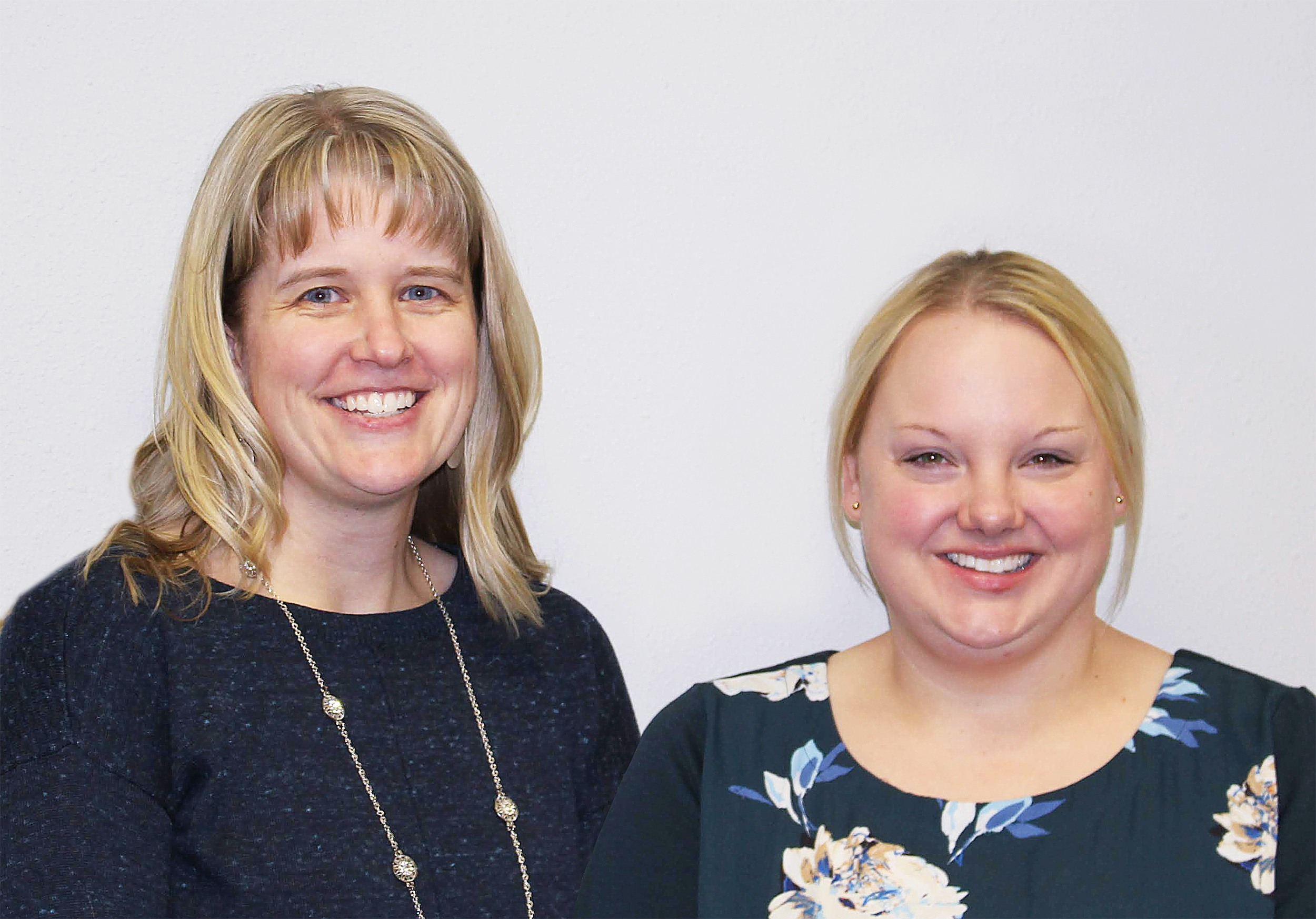
The heart of the office is the administrative staff up front. Two full time administrative assistants April and Beth, handle the bulk of the documentation, record keeping, and reception duties. They also ensure that the quoting process is carried out consistently and efficiently.
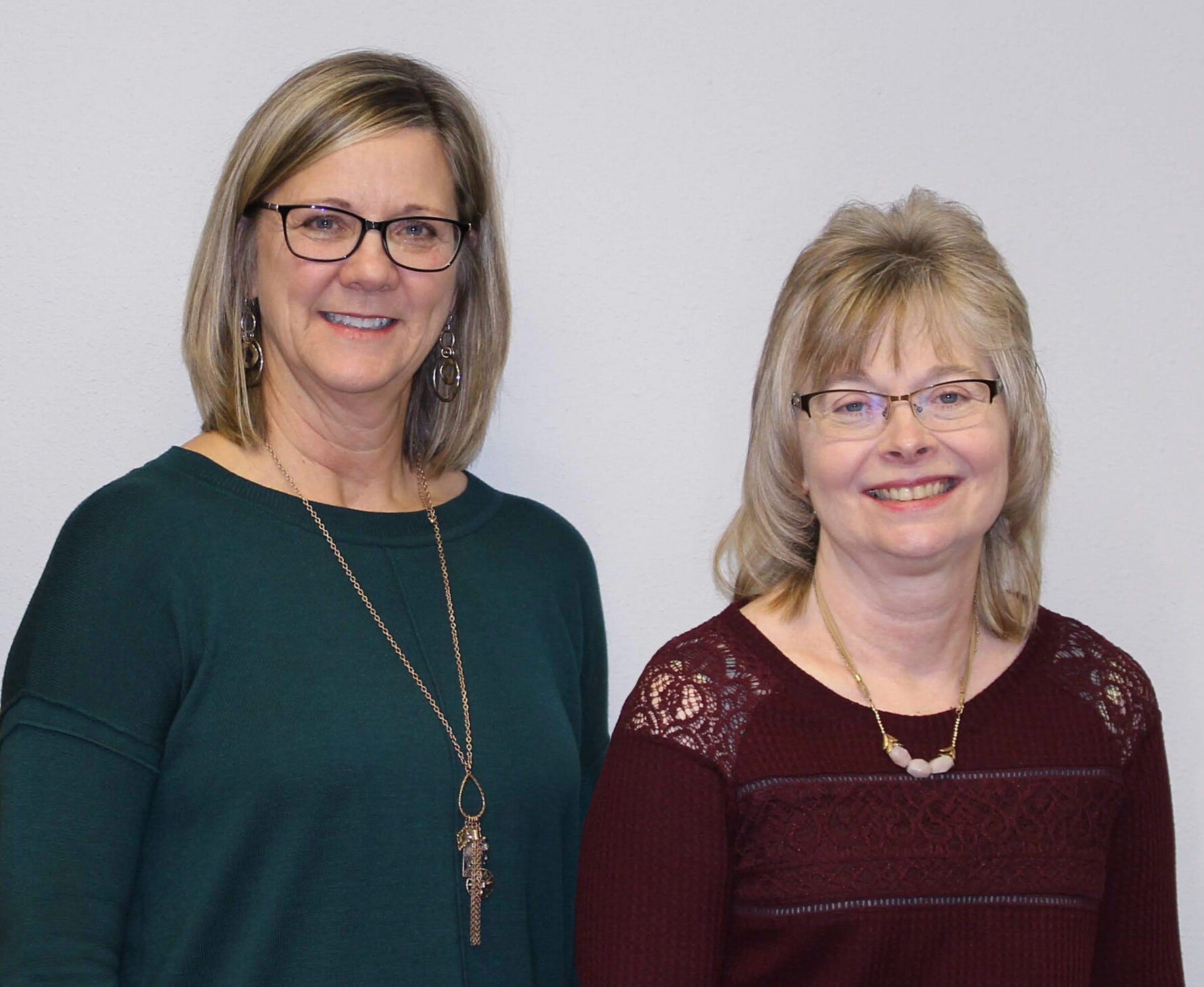
Accounting, billing, compliance, and quote verification, and other duties, are shared by three more office employees, Lorie, and Carol. Any quote that Ranco provides is double-checked through the front office to ensure accuracy and consistency.
Electrical
Ranco’s electrical department is very important to the success of the company. With the fast pace of technology and new ideas being developed every day, Ranco comes to the forefront to lead our industry in this endeavor. All of our control panels and electronics are tested and built here with meticulous care.
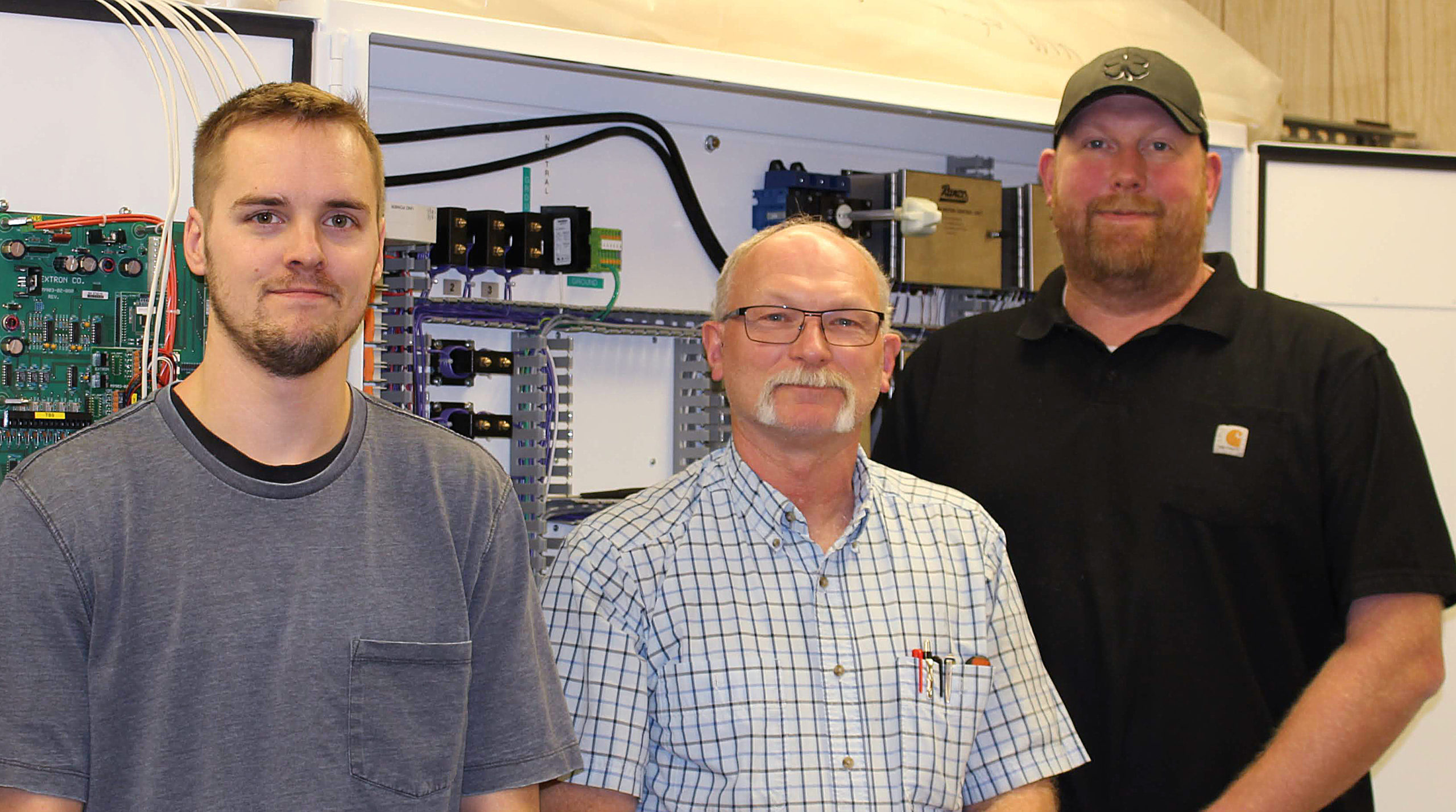
With many years of experience directly devoted to Ranco and its operating system, along with direct customer interaction, the team includes Nick, Mike and John
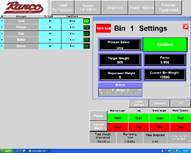
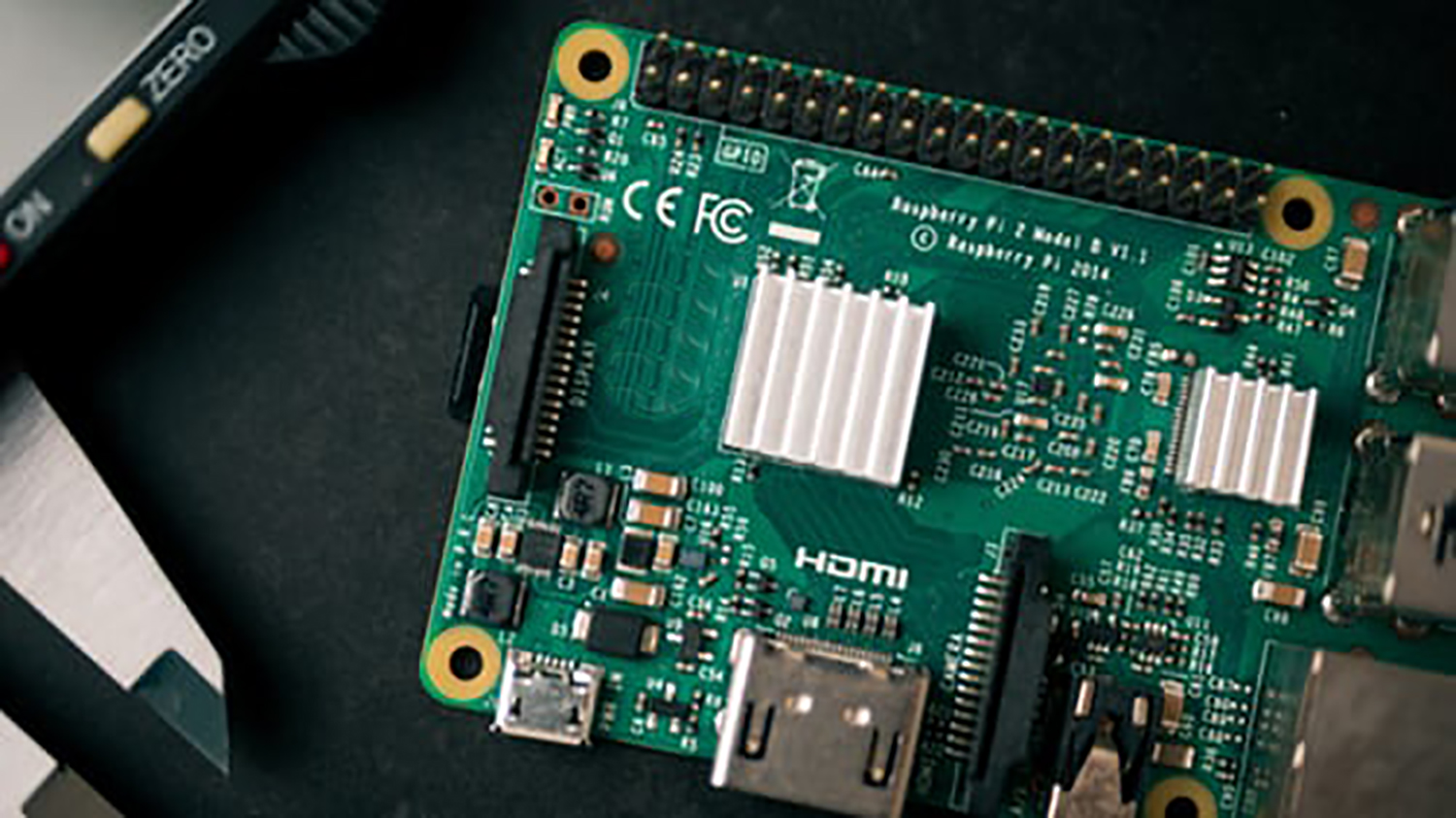
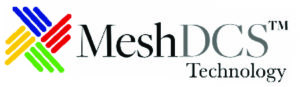
Product development, product improvement, and new product innovation happens through the electrical department consistently. Much of our research and product development occurs here. Minor improvements occur continually because of the attention to detail in the department.
Whenever we sell a blend system the Ranco electrical technicians travel to the site for final connections, system calibration, and a training period. The training that the electrical department offers is thorough and will set you up for a successful experience with a Ranco blend system. Ranco is dedicated to making sure your system is running correctly before leaving your site.
Finally, our electricians are always available to take a troubleshooting call. With the MeshDCS operating system, many of the calls can be done remotely and in ‘real-time’. With your approval, our technicians will be able to see your system from our location to better diagnose any questions you might have. They are experts at the operation of our blend system and can talk you through any issues that you might have.
Drafting
Ranco has a fully staffed in house drafting department. Nearly every system or equipment quote that Ranco sends has been drawn in AutoCAD to ensure compatibility and proper fit. All of Ranco’s drafting staff are qualified and experienced. Whether you are planning a plant add-on, redesign, new plant, or just an additional piece of equipment, the Ranco drafting team is very valuable.
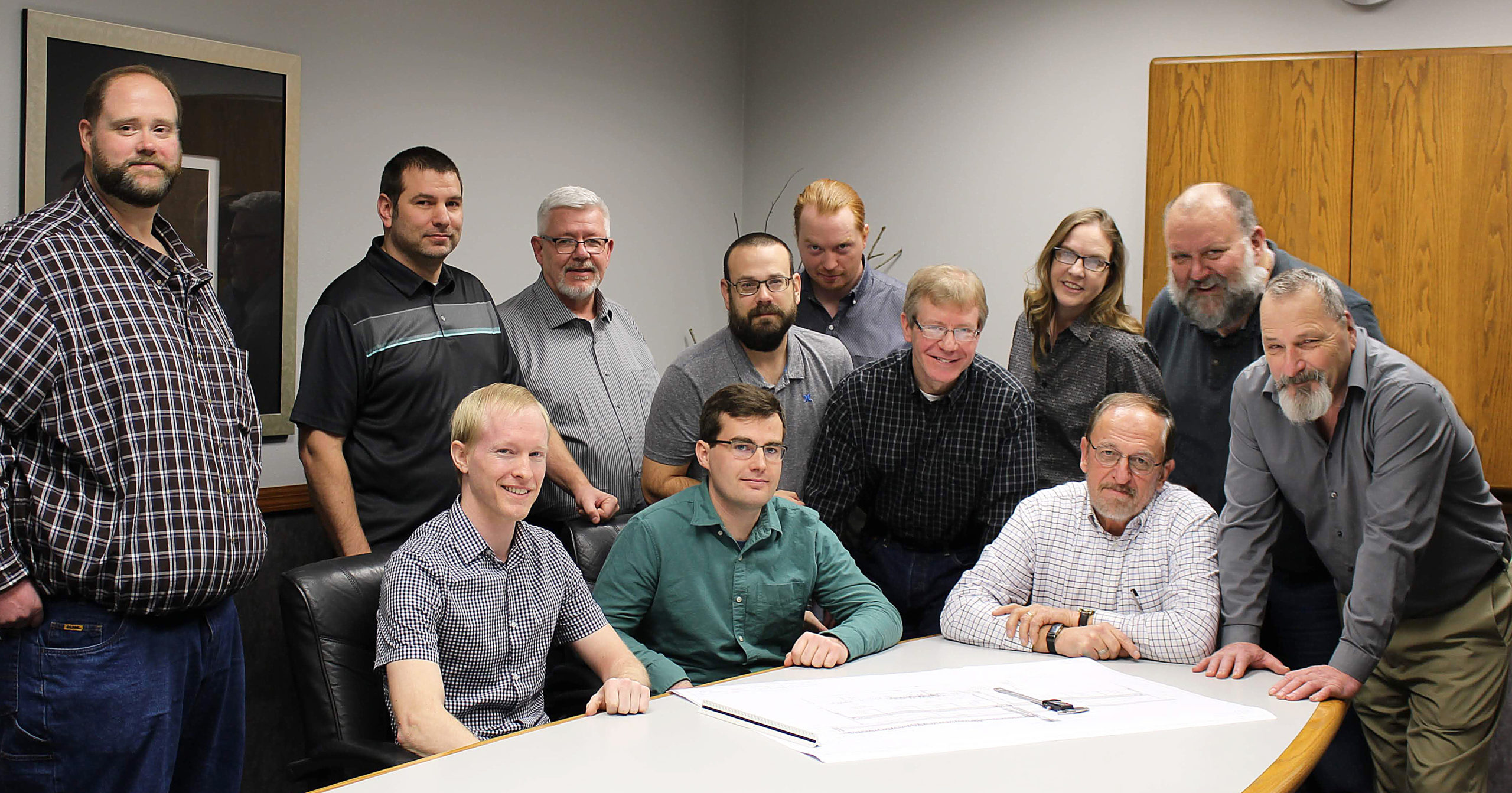
Ranco’s drafting staff has detailed every equipment part that we sell to ensure consistency in manufacture and replacement if necessary. They also play a crucial role in our research and development process. With employee longevity throughout the company, the drafting department capitalizes on the experience to avoid unnecessary steps or time to complete the project. Any new concept is drawn up right away to show if it is viable. If so, we can produce it accurately the first time, reducing the lead time for new products and technology to market.
If you are planning a new plant, contact Ranco and allow our drafting team to put together a building sketch that will meet your storage requirements and dimension requirements. Ranco building concepts are a huge benefit to your project. With nearly sixty years of experience, we have installed equipment in many different types of buildings, and we know which building designs and dimensions are most cost effective and user friendly. A Ranco building concept sketch will allow you to receive competitive bids for contractors or identify building dimensions for companies that are experienced in this type of construction.
Engineering
Having an experienced engineering group on staff allow for accurate and safe equipment configurations and correct building specifics. Along with the project managers and drafting team, the engineers, Jesse, David, Justin and Greg, using their experience, can add that element of problem solving to the design related to codes and building requirements. This assures a project that works as it should.
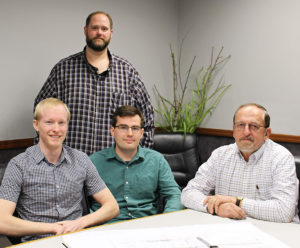
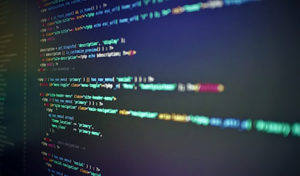
Fabrication & Manufacturing
The shop is the heart of Ranco. All of our equipment is manufactured in Sioux Rapids, Iowa at our single location.
Four buildings make up our shop. Support structures, catwalk, blenders, rack and pinion gates, and hoppers are all built in our west shop. The east shop handles conveyors, u-trough augers, platforms, car unloaders, and drag chains. One building is dedicated to the construction of our bucket elevators. Finally, our downtown “RanTec” building is where the bulk of our machining, heavy breaking, plasma cutting, and parts manufacturing occurs.
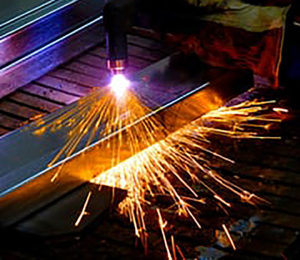
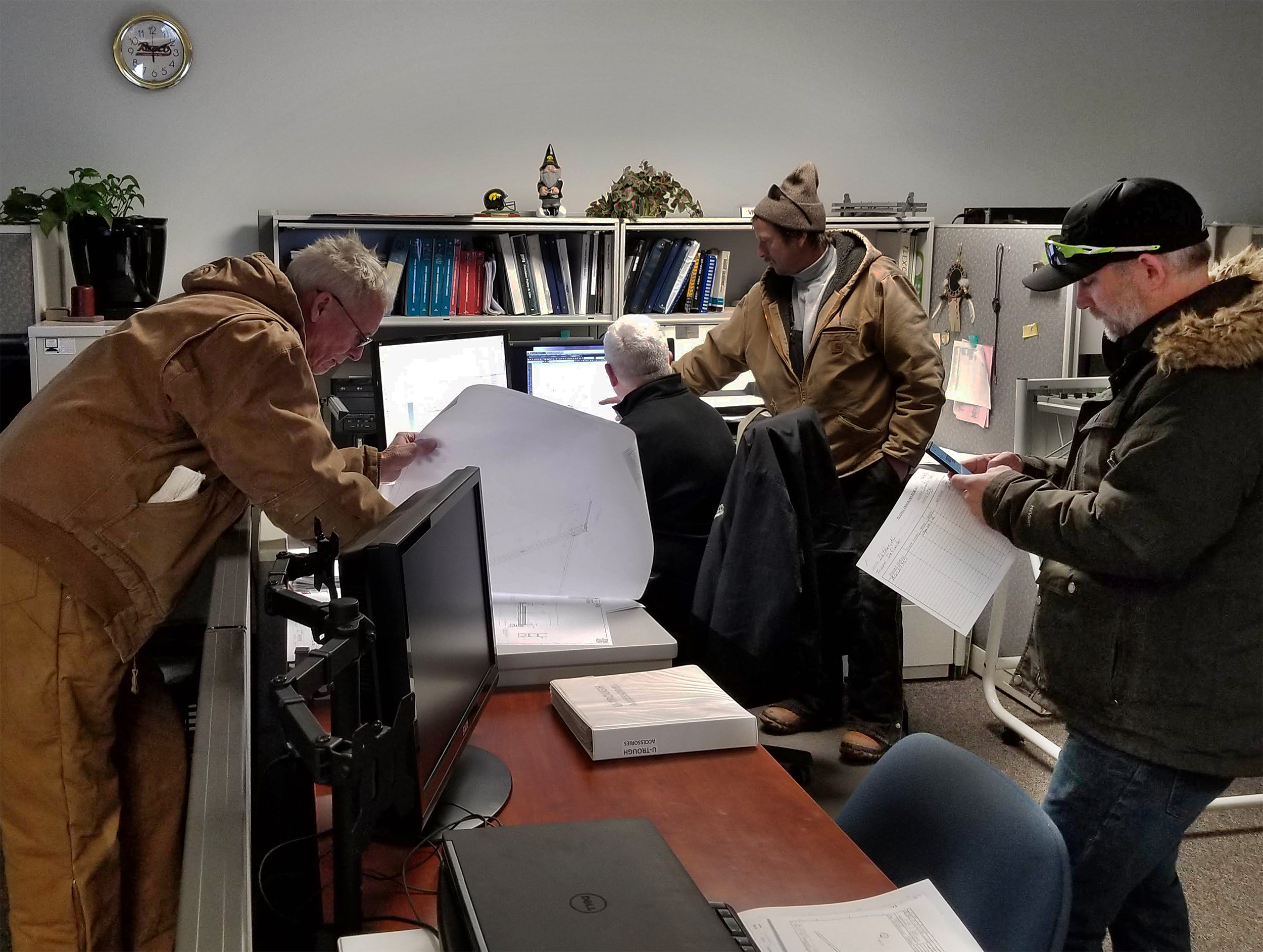
The shops work stations communicate together seamlessly to ensure timely production and delivery of equipment to the customer.
Ranco is fortunate to have extremely talented and dedicated employees. Some have been with Ranco for over 40 years. Some might say it’s the Midwest work ethics, but the quality and workmanship that the shop strives for is second-to-none in the industry.
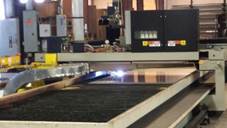
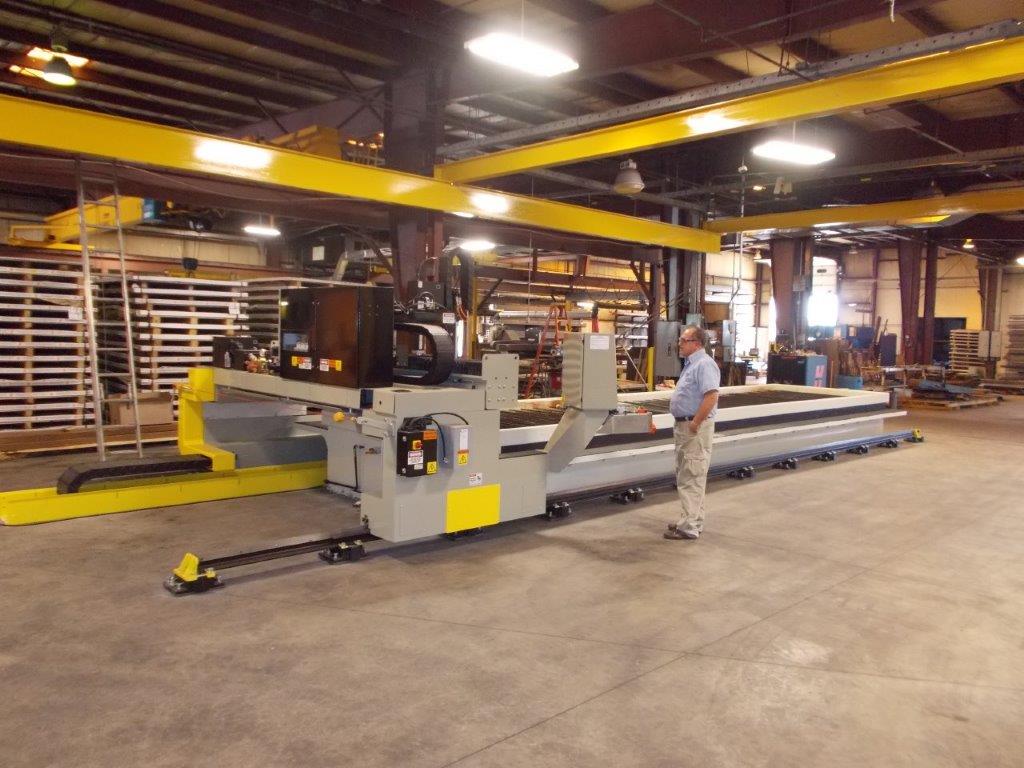
Paint
The paint shop at Ranco is a key component in the production line. The shop layout, track system, and ventilation system was designed completely in house to meet our high volume needs. We utilize a chemical washing process to prepare for the painting process to provide a long-lasting paint bond. Also, much of our steel is completely sandblasted before the painting process begins.
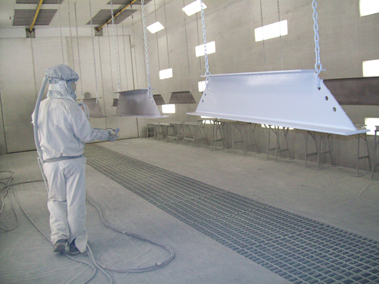
Fiberglass
Ranco has been utilizing fiberglass in the product line since the company began. Fiberglass is often overlooked, but is a perfect material for the fertilizer industry. Fiberglass never rusts or corrodes, is strong, light, and easily repairable if needed.
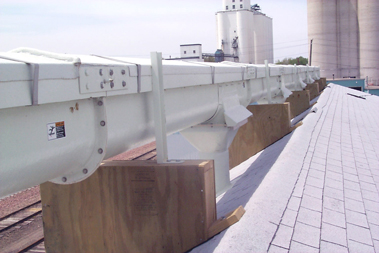
Ranco is unique in that we maintain a fully staffed fiberglass shop. Most of our weather cover is produced here, as well as several styles of hoppers, conveyor dump boxes, telescoping unloading spouts, and protective covers and guards. It is reasonable to say that Ranco has one of the most experienced and talented fiberglass teams in the Midwest with an excellent warehouse of molds and equipment needed to make excellent fiberglass products.
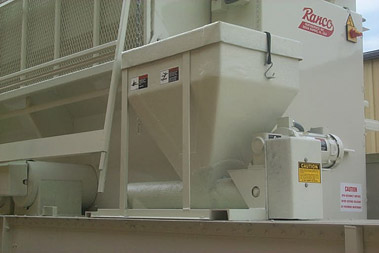
Parts and Shipping
Ranco maintains a fully stocked parts department on our site. We stock equipment like Baldor and Dodge drive and bearing components, a full line of drive belts and bearings, bolts, nuts and washers, as well as all the needed parts to complete a full installation for our crews.
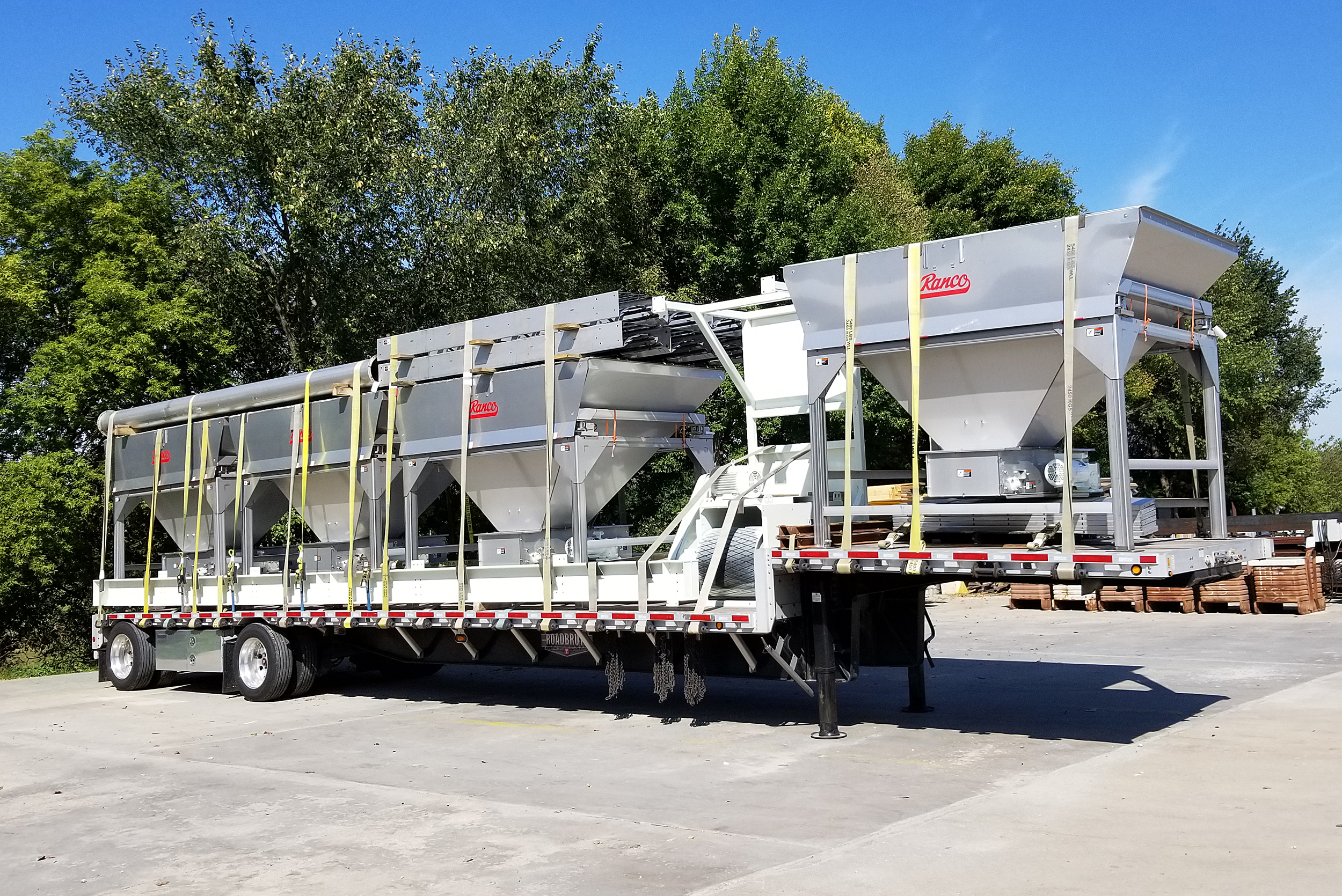
Years of managing our inventory has put us at the top of the industry in terms of having replacement items in stock for all common issues. Nate, Kyle and Brittanie in our shipping department prides themselves on speedy and accurate order preparation. If we receive a parts order by early afternoon, the chances are we can get it to you the next day utilizing UPS next day delivery.

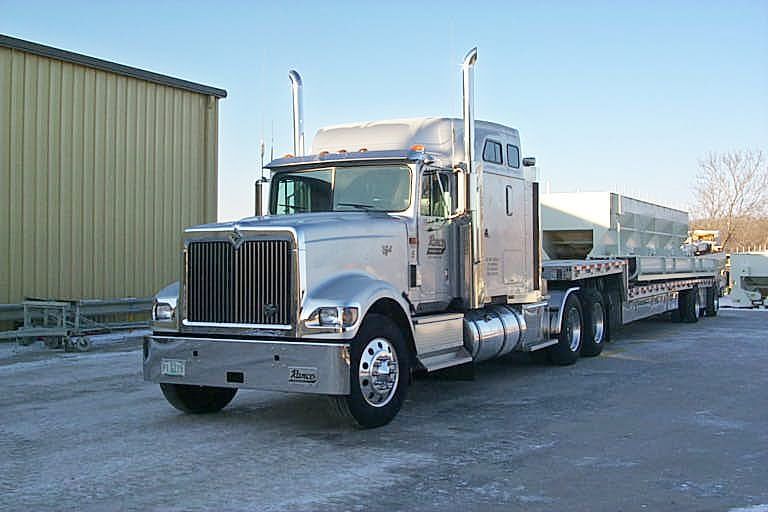
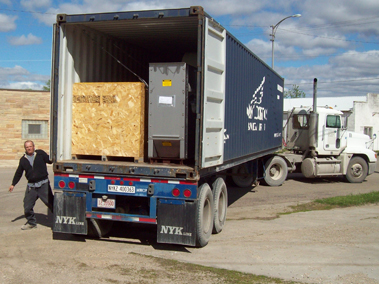
Our goal is to provide the service you need to keep running. With the shipping department, there are several ways to get products to you which include UPS, FedEx, USPS, Ranco trucks or outside trucking services. And in some cases, the project manager or installation crew may be able to bring parts on their next visit to your site. With these options, the Ranco shipping team can find you the best, most efficient and cost-effective service for you.
Installation Crews
Ranco is one of the few, and possibly the only fertilizer equipment company that has utilized its’ own installation crews from its’ inception. This means that our crews understand all of the ‘ins-and-outs’ to installing our equipment correctly the first time and in an efficient manner. Our crews are trained not only in the quality of installation, but also customer relations and respect of the customer site.
With years of experience with our equipment, the installation process runs smoothly and efficiently. Our crews normally work 10 hour days or more, while communicating with the customer and other contractors as needed or requested. Operating several crews around the country on a regular basis, it is important to make sure we complete the projects in a timely manner and that the project is satisfactory at completion.
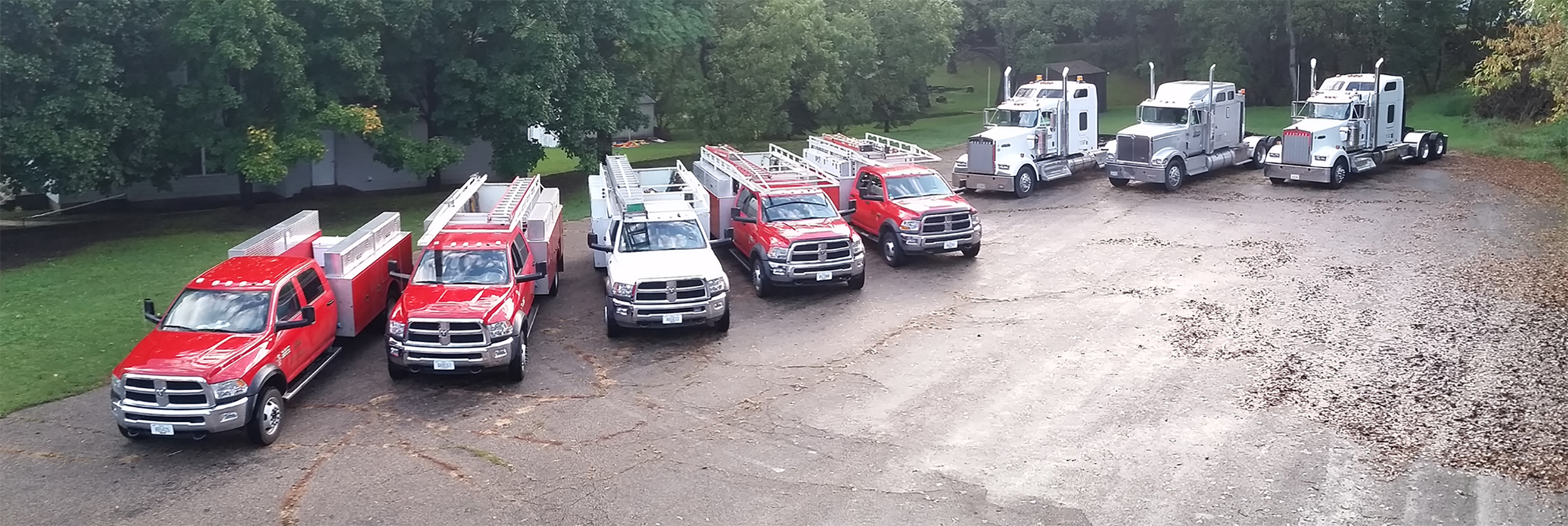
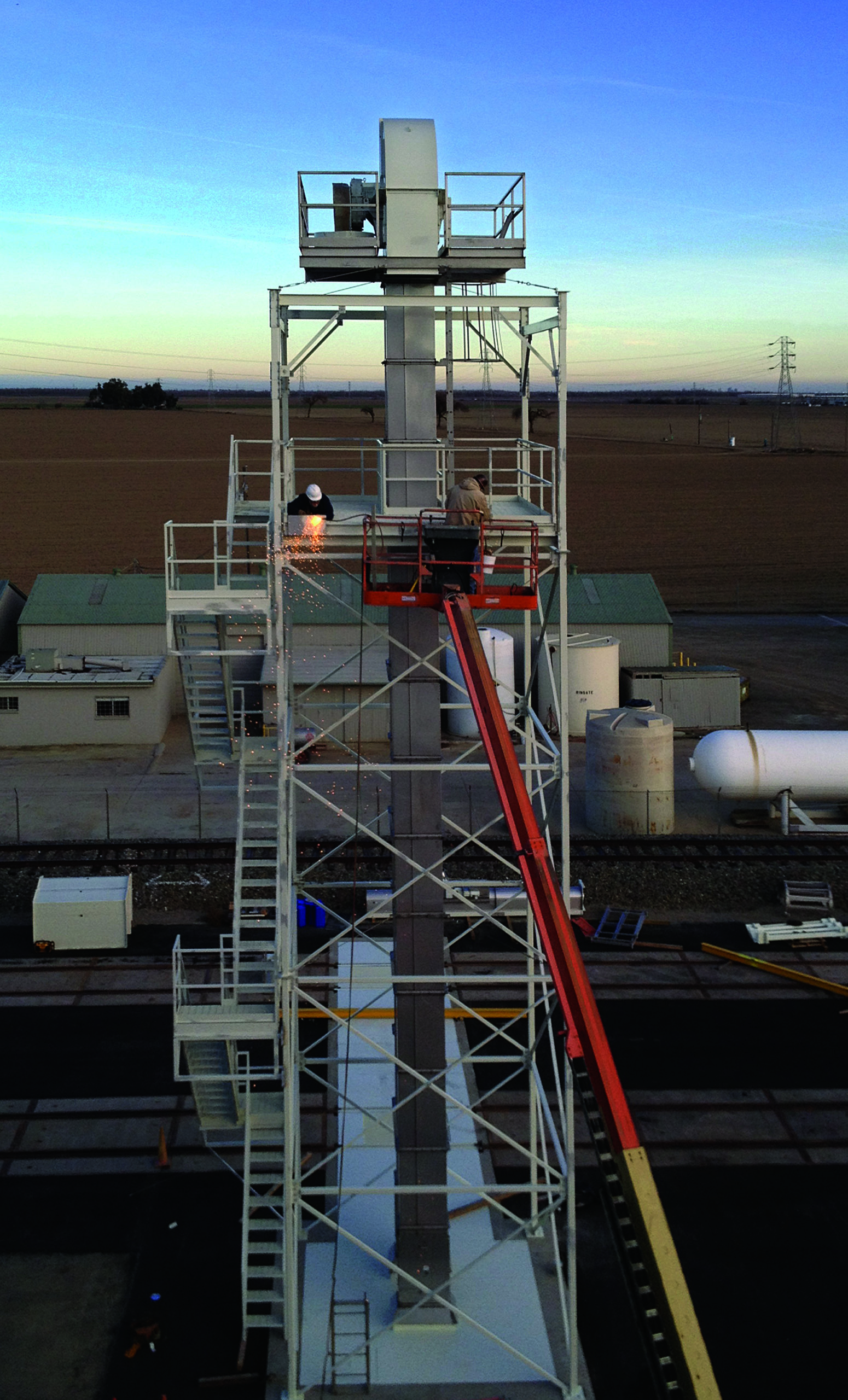
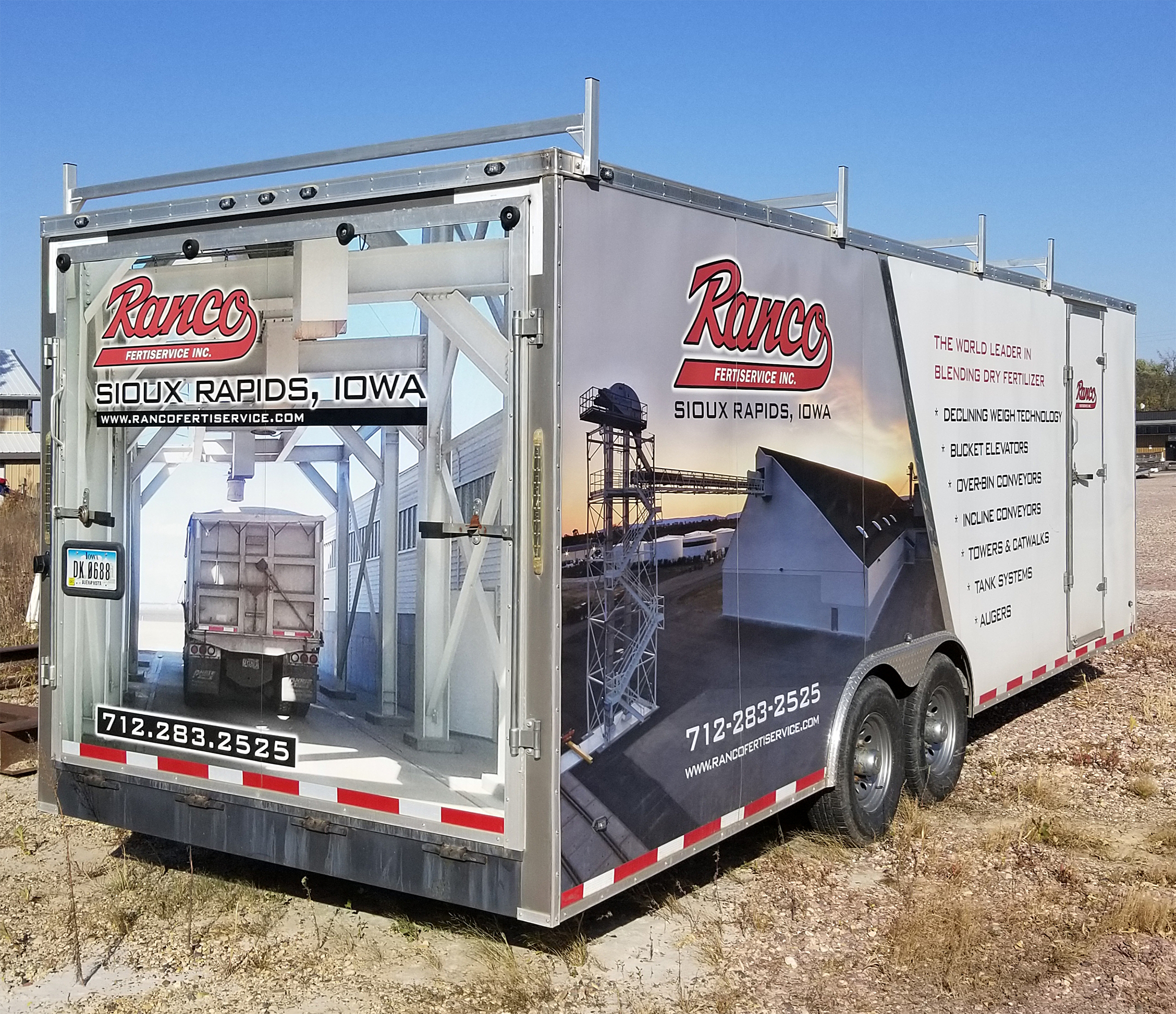
